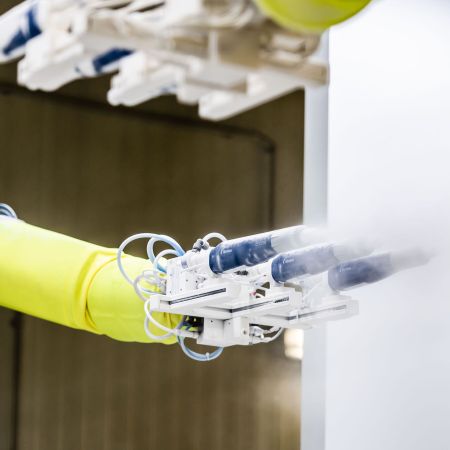
Powder coating
Pre-treatment
Pre-treatment and its correctly chosen method are the main prerequisites for achieving the desired corrosion resistance of the coating. Variables such as the nature of the contamination and its intensity determine the choice of the appropriate method. For any paint application, the workpiece surface must be grease free and the surface must be dry. Depending on the degree of contamination of the substrate and the desired corrosion resistance of the finish, different scenarios of chemical pre-treatment are scheduled and suitable blasting medium is used.
For most of the types of chemical pretreatment, i.e. deoxidation, degreasing, phosphating, rinsing, demi rinsing and passivation, we provide continuous wash tunnels, immersion tanks and manual wash booths. This also includes equipment for liquid solution circulation and a demin plant. Wastewater facilities for environmentally friendly disposal of rinse water are also part of the pretreatment technology. The equipment can either be included in the line or delivered separately.
Wastewater treatment plant
When designing the surface treatment technology, it is important to take into account the subsequent disposal of wastewater (especially from the chemical pre-treatment). With respect to this important aspect, we are able to deliver wastewater disposal facilitiy as part of the supply of the entire project or separately to the already existing technology. Wastewater treatment plants come in various configurations, from manual to fully automatic. The wastewater treatment/disposal process is always adapted to the required parameters and local effluent limits set by the competent authorities at the installation site.
The treatment plants may include optional accessories such as end-of-pipe sand filtration, activated carbon filter or multi-step pH measurement with fully automatic dosing of chemicals needed in the neutralization process. The entire wastewater neutralisation process is recorded within the technology control system.
The installation of the wastewater treatment plant will considerably reduce the operating costs of external wastewater disposal.
Drying and polymerization ovens
Polymerization ovens are used for curing or gelling powder paints. Drying ovens are used for products coming from the wash-based pretreatment sections. The ovens can be of the chamber or tunnel type. Heating can be electric, natural gas, PLG or light fuel oil. The products can be loaded into the furnace manually by means of loading trolleys or by means of an overhead or floor conveyor, or by other systems should the technological plan require.
The dimensions and power of the furnaces are determined by the capacity and dimensions of the products to be treated.
Infrared ovens
Gas catalytic infrared ovens
The reasons why the powder coating industry is looking for more economical and efficient solutions regarding the curing process are mainly due to more efficient use of energy and cost reduction. For thick-walled products, gas catalytic infrared ovens have been proven to be "greener", more cost-effective and more efficient than conventional ovens, while significantly reducing the carbon footprint of the curing process.
KEY BENEFITS:
- rapid increase of product temperature;
- lower operational costs;
- precise temperature regulation;
- no cross contamination of the paint coat;
- takes lower size of floor space;
- environmentally-friendly - no NOx or CO emissions.
IT'S WORTH THE INVESTMENT:
Heraeus modular systems use fully reflective IR technology and a so-called Gas Pulse Systém to control a steady an evenly distributed temperature inside the oven, thus ensuring the quality of the output for a variety of products; moldings, castings, sheet metal, tubular or angle weldments.
HOW IT WORKS:
Gas catalytic infrared technology is a flameless heating technology that produces uniform, low-intensity, non-heat heat. This mid-wavelength energy is easily and evenly absorbed by a wide range of materials, including powder paints. Faster absorption also means faster curing than traditional convection ovens. Catalytic infrared furnaces can be used as heating accelerators prior to conventional convection furnaces, or stand alone solely for curing of coatings.
Intuitive touch control for comfortable adjustment of the curing cycle. PLC-controlled gas pulsation system controls the heating profile. This means that all heating profiles can be stored and recalled. The wattage of each zone in the furnace is easily adjusted via the touch panel for each zone individually. The furnace control also includes remote access over the internet for control software updates and technical support.
The Gas Pulse System technology is used to control the heaters individually. The system doses a pre-set amount of natural gas, which is then consumed in a flameless reaction in the heater.
The patented catalytic heaters, which are environmentally friendly, significantly reduce the carbon footprint while eliminating NOx and CO production during the curing process. The by-products of the flameless reaction are CO2 and water vapor, which are sucked out of the furnace space.
Coating booths
Powder coating booths are made of polished stainless steel or antistatic PVC.
Depending on the size of the product to be coated and its hanging solution, the booth can be of a load-in, floor or continuous type. Powder paint can be either lost to overspray, or recycled using a high efficiency cyclone. The application of powder in the application booth can be done manually, automatically by gun movers, or by robots.
The design and function of the coating booth is always designed depending on the type of production and customer preferences.
Coating systems
Powder paint application can only be done using either electrostatic, or electrokinetic applicators. Our supply features equipments that are easy to use and achieve excellent surface results.
System types:
- manual;
- automated with gun movers;
- robotic;
- quick color change system within 2 minutes.
We will help your find the best solution to your paint shop, be it choosing a new piece or running an overhaul of your current applicator.
Choose from a wide range of accessories that fit all types of surfaces.
Conveyor systems
To move products between individual facility units, the option of a manual or automatic conveyor is available for surface treatment. Manual transfer can be carried out using push carts, roller conveyors or overhead conveyors. The automatic conveyor uses a single track or a double track system, i.e. Power & Free.
Power & Free conveyors allows to release or stop individual trolleys at any given time and to disengage or accumulate trolleys at various points within the conveyor system.
To handle heavy products, the conveyor system is fitted with a loading and an unloading station.
Accessories
In addition to painting equipment, we also offer a wide range of accessories and various types of inspection instruments.
All our range of accessories can be found in our e-shop.