Coating Thickness Gages and Inspection Instruments
Quality control is an integral part of the painting process. With an optimal set up of quality control and with quality measuring instruments, we can reduce rejects or complaints and get a better overview of the entire painting process. As a result, we save material, energy and time. Enclosed with the measuring instruments is the Certificate of Calibartion so they can be put into operation immediately. They come in durable cases, the menu is user-friendly and connection to a PC with automatic data download and reports.
Coating thickness gages for metal substrates
Coating thickness or dry film thickness (DFT) is the key variable in the quality of the final product.
Dry film thickness (DFT) or coating thickness is a crucial step during application and output control of quality of protective coats. The coats perform best when the DFT corresponds with the manufacturer's specifications. Correct surface thickness ensures the best quality of the final product. Even with the most basic specification, one cannot do without DFT measurement.
A regular thickness control helps to optimize costs, control application effectivity, and maintain quality of the surface treatment and to meet specifications stated in the contract. Protective coatings manufacturers recommend to adhere these specifications to attain the best performace and the end users expect these parameters to be met.
The main division of the thicknes gages is based on the type of the substrate that is to be coated. The most common substrate subjected to surface treatment is steel. Steel has feromagnetic properties hence the thickness gages use the principle of electromagnetic induction. Coats on nonferrous metals such as aluminium, copper, brass are measurable using the method of eddy current testing.
Coating thickness gages "DeFelsko PosiTector" are able to test layer thickness within the range of 0 to 63,5 mm.
Thickness gages by DeFelsko (US) meet the highest demans on accuracy of measure and user-friendliness
Coating thickness for non-metal substrates
Measurement of film thickness on plastics, glass, ceramics or concrete used to be a hard task and it was only possible to accomplish it only by destructive methods. An angle cut of 45° or a perpendicular cut followed by an assessment using a microscope.
Thanks to the ultrasound thickness meter it is now feasable to measure film thickness over non-metal substrates non-destructively.
The gage sends and recieves back ultrasound waves that go through the layers to the base surface. As long as the boundery between the base substrate and the film is discernable, the thickness of the film can be determined.
Gloss measurement
Gloss meter is a device that uses surface gloss to measure its reflectace.The gloss intensity is determined by reflecting a light beam of constant intensity, and angle onto a surface and subsequent measuring of the amount of light reflected back at the same angle.
There is plenty of way how to measure gloss intensity based on the surface properties. With non-metals, such as plastics, the intesity of reflected light grows with increasing the light beam angle as part of the light is absorbed by the film, or is difused based on the film's color. Metals, on the other hand, shopw much higher reflectance and thus they are less dependent on angle of incidence.
There are many international technical standards that define the application and specifications for different types of gloss meters used on different types of materials including paints, ceramics, paper, metals and plastics. Many industries use glossmeters in quality control to measure the gloss of products to ensure consistency in their manufacturing processes. The automotive industry is a major user of gloss meters with applications ranging from production halls to repair shops.
The glossmeter provides a quantifiable way to measure gloss intensity ensuring consistency of measurement by defining precise lighting and viewing conditions. The configuration of the illumination source and observation angles allows measurements over a small range of total reflection angles. The results of the glossmeter measurements are related to the amount of light reflected from a black glass standard with a defined refractive index. The ratio of reflected to incident light for the sample compared to the ratio for the gloss standard is recorded as gloss units (GU).
The measurement angle refers to the angle between the incident light and the perpendicular. Three measurement angles (20°, 60° and 85°) are specified to cover most industrial coating applications from high gloss to matt.
Uncured coating thickness
Measuring the uncured coating thickness and predicting its thickness after curing is a complex application. Fortunately, there are nowadays ways to determine these values. We have a choice of the ultrasonic method and the method of measuring the surface temperature after the flash. Each of these methods has its pros and cons.
The ultrasonic method is relatively inexpensive. Its primary limitation is a maximum coating thickness of 100 µm and it is only useful for powder coating. However, its affordability makes it an excellent tool for smaller paint shops as well. These products are represented in our range by the DeFelsko PosiTest PC, which is the most advanced device available in the field of ultrasonic devices for measuring uncured powder coatings.
Flash method instruments are more expensive to purchase. On the other hand, they offer a range of up to 400 µm and are also suitable for wet painting. A representative of this group is the Swiss Coatmaster Flex. The company Coatmaster has patented this method of measurement and it is the most comprehensive instrument for measuring uncured paint thickness, both powder and wet, in the world.
Wall thickness measurement
Ultrasonic wall thickness gages (ultrasonic thickness gauges, ultrasonic thickness testers, ultrasonic thickness meters, UT gauges, etc.) measure the wall thickness of materials such as steel, plastic, and more using ultrasonic technology. . Ultrasonic Thickness Gauges are ideal for measuring the effects of corrosion or erosion on tanks, pipes, or any structure where access is limited to one side. Multiple echo Thru-Paint models (UTG M) and UTG P) measure the metal thickness of a painted structure without having to remove the coating.
Ultrasonic thickness measurement techniques are used to measure a wide range of substrates and applications for loss of material thickness due to corrosion or erosion. Ultrasonic Thickness Gauges are designed for measuring the thickness of metallic (cast iron, steel, and aluminum) and non-metallic (ceramics, plastics, and glass) substrates and any other ultrasonic wave-conductor provided it has relatively parallel top and bottom surfaces.
An ultrasonic thickness gauge facilitates rapid inspection of the thickness of large metallic structures at small measurement intervals, providing a high-detail thickness map of a scanned surface. When access is only available from one side of the substrate, ultrasonic wall thickness measurement is the most efficient way to monitor the effects of erosion or corrosion and is instrumental to both quality assurance and quality control.
Environmental monitoring
The environmental conditions during pre-treatment and application of a coating system are major factors affecting the long-term performance of coatings on steel structures. Dew Point Meters can be used to monitor environmental conditions before, during, and after painting. Ideal for surface preparation as required by ISO 8502-4, an electronic Dew Point Meter determines the likelihood of dew forming on structures which are being painted.
DeFelsko offers three types of meters to measure environmental conditions: dew point meters, wind speed sensors, and infrared thermometers.
Adhesion testing
Adhesion testing using tensile pull-off strength evaluates how strong is the adherence of the coating to the substrate. As common substrates count metals, plastics, concrete, wood and glass. Paints, varnishes, coatings differ significantly and encompass powder coatings cured by UV light, ceramics, epoxides, bitumen (tarmac sealers), thermoplastic resins (polyethylene, vinyl polymers, liquid plastic), lamination bonding agents, varnishes, resins (urethane, hydrofluorcarbons, phenols and polyesters), elastomers and anorganic substances (glass, zinc and lead).
Adhesion testing can be used as part of quality control, but more commonly it is emloyed to meet industrial standards and client's specifications. The level of ashesion depends on the coating application. Whether it is merely consumer goods or a construction industry article, an early adhesion failure with means extra costs.
Salt contamination test – Bresle method
Prior to application of protective coating, steel substrates must be thoroughly cleansed to ensure the coat fulfills its purpose and to prevent premature degradation. A common way to prepare a surface ready to be coated is by abrasive blasting to remove oxides and previous coats. A bare steel surface is susceptible to water-solulable salts that are omnipresent.
Dissolved salts are not visible to the naked eye. Salt deposits on the substrate can absorb moisture through the coating which can later result into degradation of the product due to osmotic blistering or disbondment. In some cases, the abrasive medium itself might be contaminated with water-solulable agents such as chloride or suphate salts that are furtherly transferred onto the bare steel surface causing a premature coating failure.
Surface profile measurement
Steel is often abrasive-blast cleaned or otherwise roughened prior to painting. The peak-to-valley height of the resultant "surface profile" is a critical and determining factor in the performance of applied paint and other protective coatings. A surface profile height that is too low may reduce coating bond strength (adhesion). Too high and the peaks may receive insufficient coverage leading to premature rusting and often require additional paint (and labor costs to apply it) to cover the anchor profile.
Rozvíjející se výzkum za posledních 15 let ukázal, že výška profilu povrchu není jediným důležitým parametrem. Emerging research over the past 15 years has shown surface profile height is not the only important parameter. Peak density (also known as peak count), the number of peaks in the surface profile per unit area, has been shown to be a strong determinant of coating adhesion and resistance to corrosion. In fact, studies have found that peak density may be a better predictor of coating performance than peak-to-valley height.
Surface profile height can also be relevant for other industries, as a way to quantify the profile height of non-skid surfaces, and to evaluate the Concrete Surface Profile (CSP) prior to applying coatings on concrete.
Concrete moisture measurement
Before applying a protective coating or other flooring materials to a concrete slab, it is critical to ensure that the moisture level inside the concrete has decreased to acceptable levels—typically ≤75% Relative Humidity (RH), or ≤5% Moisture Content (MC).
If not, moisture can accumulate below the coating or flooring causing discoloration, cupping, buckling, blistering, adhesive failure, and/or mold growth. There are various methods used for concrete moisture measurement.The two most-common methods utilize non-destructive electronic impedance meters (ASTM F2659) or in situ relative humidity probes (ASTM F2170).
Proper inspection of the moisture content in concrete before installing a flooring system is a necessary part in quality control and assurance—lowering the chances of a flooring system failure.
Porosity in coating – pinhole detectors
After a protective coating has been applied, it is important to ensure there are no defects or discontinuities present that expose the substrate beneath. Small areas of thin or missing coating, called 'pinholes' or 'holidays', can become foci for corrosion and drastically reduce the life of a protective coating system. A pinhole detector is a non-destructive instrument used for detecting discontinuities in a coating system including holidays, pinholes, and cracks.
DeFelsko offers two types of porosity detectors: low voltage (wet sponge tester) and high voltage (spark tester). Low voltage detectors, like the PosiTest LPD, are typically used on paint systems less than 500 µm (20 mils) thick. High voltage holiday testers, like the PosiTest HHD operate at voltages up to 35,000 V and are typically used on coatings at least 200 µm (8 mils) thick.
Hardness testing - Shore, Barcol
Hardness can be defined as a material's resistance to indentation. Hardness testing is an important step in many industries around the world, including metals, fiberglass and plastics; it is often used to certify quality of materials, test repairs, and can indicate potential coating failure.
DeFelsko offers digital and analog hardness tests in compliance with three different recognized hardness test methods: Shore and Barcol. PosiTector SHD Shore Hardness meter is eirhet available in Shore A, or Shore D to measure indentation hardness of non-metallic materials. PosiTector BHI Barcol Hardness Impressor is an ideal instrument to measure indentation hardness of soft metals, harder plastics and fibre-reinforced plastics.
Temperature profile measurement
Correct setting of the curing temperature is crucial to achieve the declared parameters of the applied paint. Whether these parameters are functional or visual. In the case of complicated geometry of a product, it is not easy to detect improper curing of the product and, in the worst case, we can only find out about it from subsequent claims.
Such scenario can be prevented by temperature profiling, where temperature surface probes are attached to the product and monitor the temperature throughout the curing process from its start , the product's ability to retain temperature, until the product has cooled down. Measurements are taken both on the surfce of the product and its immediate proximity.
Dataloggers endure temperatures up to 300°C for 100 minutes.
Color evaluation
The spectrophotometer for colour appearance control is used to measure and quantify the colour qualities of coatings and materials. Its operation is based on the principle of reflection of light by the sample and subsequent evaluation of this spectrum.
The basic feature of a spectrophotometer for colour appearance control is a light source that emits light of a known wavelength spectrum. This light is guided through a spherical optical system to the sample, which is located in the opening of the measuring chamber. When the sample is illuminated by the light, it is absorbed and reflected. Absorbance is a measured quantity that indicates how much the sample absorbs light at a given wavelength and how much light it reflects. After the light is reflected from the sample, the light is captured by the detector. The detector captures the intensity of the light for different wavelengths. This signal is then processed by a spectrophotometer and converted to a numerical value.
The result of the measurement is the reflectance spectrum of the sample for different wavelengths. This spectrum is then analysed and interpreted to obtain information about the colour properties of the sample, such as colour, hue and saturation.
In practice, a spectrophotometer for colour control is often calibrated using standardized colour samples to ensure the accuracy and repeatability of the measurements. The calibration curve is then used to convert the measured values to a specific colour.
Our range includes both fully professional equipment for detailed evaluation in the laboratory and instrumets at an affordalble price for retailers and industrial consumers.
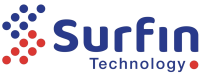