Continuous wet coating line with a manual conveyor
-
Client:Hoxter, a.s.
-
Year of implementation:2024
-
Location:Jinačovice (CZ)
-
Technical specification:
- Max Product Dimensions:
- 110 x 60 x 160 cm
- Max Product Weight: 150 kg
- Loading Station
- Automatic Suspended Chamber-type
Shot Blaster - Cleaning Booth
- 2x Manual Painting Booth
- Manual Conveyor
- Drying Oven
- Esco control system
-
Client:Hoxter, a.s.
-
Year of implementation:2024
-
Location:Jinačovice (CZ)
-
Technical specification:
- Max Product Dimensions:
- 110 x 60 x 160 cm
- Max Product Weight: 150 kg
- Loading Station
- Automatic Suspended Chamber-type
Shot Blaster - Cleaning Booth
- 2x Manual Painting Booth
- Manual Conveyor
- Drying Oven
- Esco control system
Technical Description
of the Implementation
Optimization of the Coating Process for Hoxter a.s.
Hoxter a.s. is a leading manufacturer of fireplace inserts with a timeless design, available in numerous design centers. Thanks to top-tier quality and precise technical execution, Hoxter has established itself among the best in the industry.
You may have come across their products without even realizing it.
In 2020, we built a wet coating booth for Hoxter, which enabled precise wet painting and ensured high-quality surface treatment. However, due to increasing demand, the company needed to expand production capacity and accelerate the coating process. That’s why Hoxter turned to us once again.
The result of our collaboration is a continuous wet coating line with a manual conveyor, which optimizes the production process and enables faster and higher-quality wet coating, leading to greater productivity and efficiency.
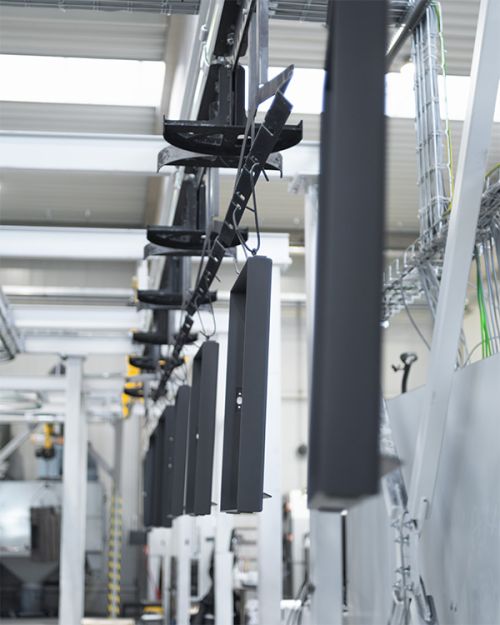
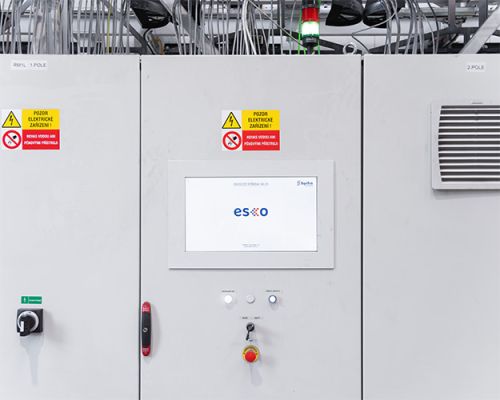
Efficient part handling thanks to a manual conveyor
With the expansion of the wet coating line, optimizing the movement of coated parts became crucial. This challenge was solved by a manual conveyor, ensuring faster and smoother transport of suspended parts throughout the coating process. As a result, painting, drying, and handling are now more efficient.
Smart Coating Line Management with Esco
One of the key advantages of the new coating line is the integration of a modern control system, providing more precise and efficient production management.
The Esco control system ensures complete oversight of key elements of the wet coating process, collects important data, and monitors the condition of filters. This system not only detects filter clogging but also alerts for scheduled replacements, minimizing unplanned downtime and extending equipment lifespan.
Let’s take a detailed look at the coating process.
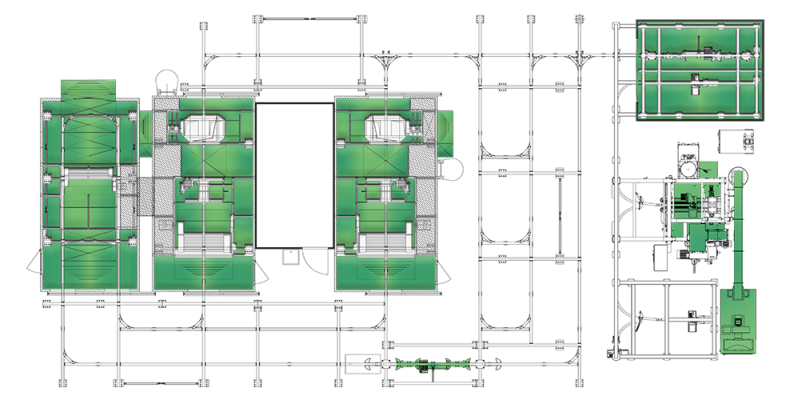

Efficient Handling
of Heavy Parts
This wet coating facility is used for the complete coating process of Hoxter fireplace inserts. Whether it’s the main fireplace unit or a door frame, the coating line must be capable of handling them safely.
To ensure an efficient hanging and unloading process, a loading station was integrated, capable of lifting parts weighing up to 150 kg. This system streamlines production and reduces the manual workload for operators.
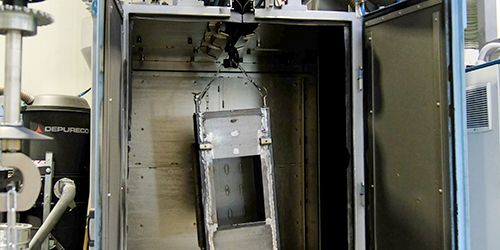
Perfect Surface
Pre-Treatment
Before Coating
To ensure a smooth and uniform surface for better paint adhesion, the coating line is equipped with an automatic suspended chamber-type shot blaster. Thanks to its integration with the conveyor system, parts can be easily inserted into the chamber, where the surface is treated with abrasive blasting.
This process removes impurities and creates an optimal base for the next stages - cleaning and coating.
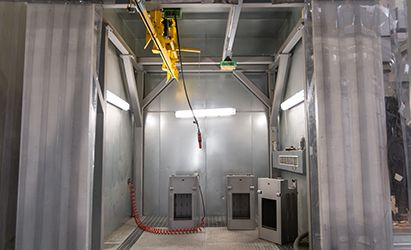
Dust Removal
for a Flawless Finish
After the blasting process, the treated part must be thoroughly cleaned. A layer of fine dust forms on the surface, which could affect paint adhesion and cause cosmetic defects.
The cleaning booth effectively removes these impurities, ensuring the surface is perfectly prepared for coating.
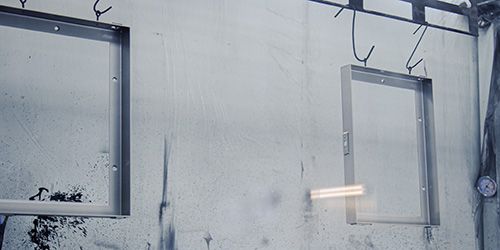
Precise Liquid Coating
To maximize the capacity of the coating line, the system is equipped with two coating booths.
Hoxter utilizes liquid coating, so the walls of the coating booths are protected by a replaceable plastic layer, which extends the equipment’s lifespan and simplifies maintenance.
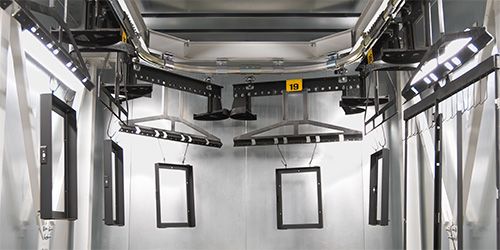
Fast Coating Curing
After the liquid coating is applied, the part is transferred to the drying oven, where the coating cures properly.
Once cured, the part moves to the loading station, where it is removed from the conveyor and prepared for final assembly.
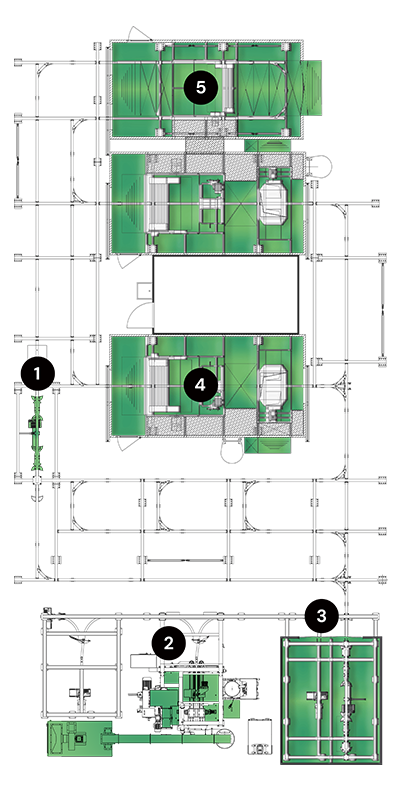

Efficient Handling
of Heavy Parts
This wet coating facility is used for the complete coating process of Hoxter fireplace inserts. Whether it’s the main fireplace unit or a door frame, the coating line must be capable of handling them safely.
To ensure an efficient hanging and unloading process, a loading station was integrated, capable of lifting parts weighing up to 150 kg. This system streamlines production and reduces the manual workload for operators.
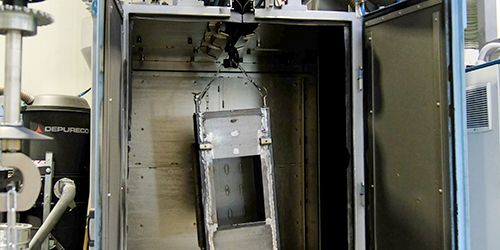
Perfect Surface
Pre-Treatment
Before Coating
To ensure a smooth and uniform surface for better paint adhesion, the coating line is equipped with an automatic suspended chamber-type shot blaster. Thanks to its integration with the conveyor system, parts can be easily inserted into the chamber, where the surface is treated with abrasive blasting.
This process removes impurities and creates an optimal base for the next stages - cleaning and coating.
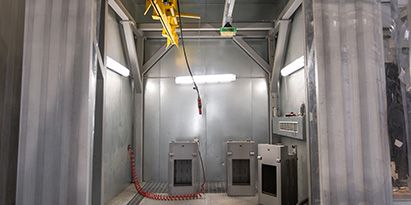
Dust Removal
for a Flawless Finish
After the blasting process, the treated part must be thoroughly cleaned. A layer of fine dust forms on the surface, which could affect paint adhesion and cause cosmetic defects.
The cleaning booth effectively removes these impurities, ensuring the surface is perfectly prepared for coating.
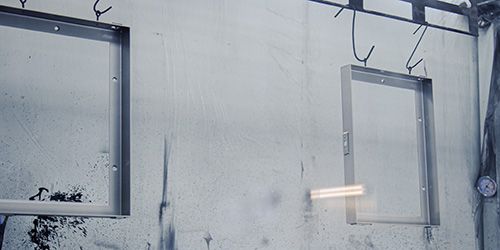
Precise Liquid Coating
To maximize the capacity of the coating line, the system is equipped with two coating booths.
Hoxter utilizes liquid coating, so the walls of the coating booths are protected by a replaceable plastic layer, which extends the equipment’s lifespan and simplifies maintenance.
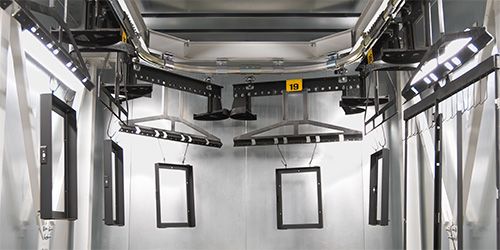
Fast Coating Curing
After the liquid coating is applied, the part is transferred to the drying oven, where the coating cures properly.
Once cured, the part moves to the loading station, where it is removed from the conveyor and prepared for final assembly.