Powder Coating Plant with Robotic Application and Automatic Trajectory Generation
-
Client:ISAN Radiátory s.r.o.
-
Year:2024
-
Location:Blansko (CZ)
-
Technical Specifications:
- Maximum Product Dimensions:
L. 4000 x W. 600 x H. 1600 mm - Maximum Product Weight: 400 kg
- Four-Stage Spray Pretreatment
- Automatic Continuous Shot Blaster
Integration of third-party equipment into the line control system - Continuous Drying Oven
- Robotic Coating Booth with Two ABB Robots
- Automatic Trajectory Generation via ESCO System
- Continuous Polymerization Oven
- Automatic Conveyor for Pretreatment
- Manual Conveyor
- ESCO Control System
- Detection of Product Position on the Hanging System
- Maximum Product Dimensions:
Technical Description of the Implementation
ISAN Radiátory s.r.o. approached us with a request to install a new coating line to replace their older production line. One of their key requirements was achieving the highest possible coating quality in hard-to-reach areas and crevices, without the need for double-layer coating. This was accomplished beyond the client's expectations, thanks to the Nordson Encore HD application technology.
Another critical requirement was to maximize the capacity and automation level of the coating process. We achieved this by integrating an automatic coating booth equipped with four horizontal spray guns on both sides and two ABB robots to pre-spray critical areas.
Digital hanging plans and advanced parametric programs ensure that each product hung on the conveyor is perfectly coated without the need for operator intervention.
The entire process is monitored and controlled by the ESCO system, developed by SURFIN Technology, which manages the coating line and oversees the entire powder coating process. This system collects production data from the hanging stage, through pretreatment, drying, powder coating, to final curing.
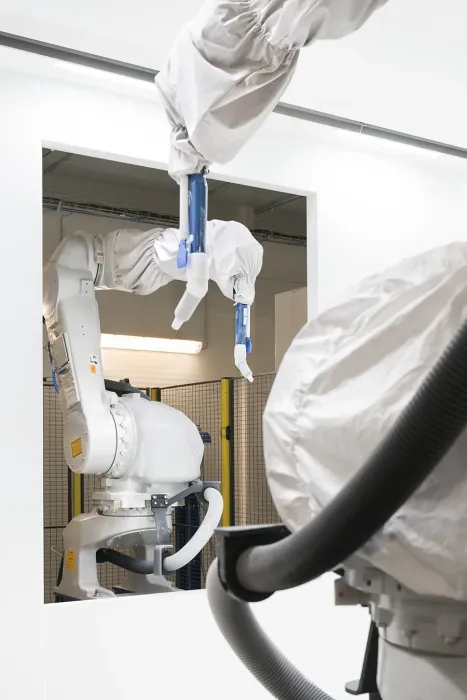